Second-generation lactic acid on the way
One of the major aims of the BE-Basic programme is to determine which non-food feedstocks suitable for the production of bio-based chemicals are available, wherever in the world they are. In flagship 1, the production of lactic acid from renewable raw materials will be studied as an example of this approach.
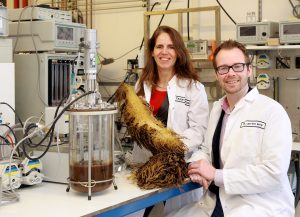
In the near future, Purac – a leading company in natural food preservation and bio-based building blocks & chemicals – wants to derive its fermentable sugars for lactic acid production from non-food sources, such as agricultural waste streams, if it can be done in a cost-effective and sustainable way. “We currently produce lactic acid from food-grade sugars, the so-called first-generation feedstock. But we want to develop a process in which we can use sugars derived from agricultural residues, the second-generation feedstock.” says Corjan van den Berg, scientist at Purac. Lactic acid and its derivatives are traditionally used as food ingredients and for certain pharmaceutical, cosmetics and technical applications. “We’re scaling our activities especially in the plastics and chemical market.”
Van den Berg’s colleague Peter Baets continued: “The plastics market is very large. For the production of bioplastics, you need a large extra volume of lactic acid, and consequently sugar as feedstock. We can’t permit ourselves to use such large volumes of food-grade sugars because that could interfere with the availability of food for human consumption. Remember the tortilla crisis in Mexico a few years ago? That was a result of an increasing demand for corn starch for biofuel.”
Choosing the feedstock
The starting point is the determination of available non-food feedstocks that are suitable for producing lactic acid. Van den Berg: “You can think of empty palm fruits, residues from sugarcane or coffee beans, and even potato peelings. It’s potentially suitable as long as it’s a non-food agricultural residue that contains enough hemi-cellulose and can be converted into fermentable sugars.”
According to Baets, there are more than a hundred kinds of waste streams in the world that are potentially of interest, considering their volume. “We can’t try them all, so we’ll have to make a considered selection on the basis of economic, technical and sustainability related criteria. Not every material is available the whole year, though. And some waste materials already have valuable applications. Many aspects play a role in this issue – which might be even more complex than we think.”
Another major issue is how to release the fermentable sugars from these feedstocks. Every waste stream might need a specific pre-treatment. Van den Berg: “It’s possible that to use empty palm fruits, you’ll need totally different techniques than when you use potato peelings.” Pre-treatment leads to the release of not only sugars but also inhibitory or toxic components. “These components can affect the microorganism that produces lactic acid later in the process. We’re therefore going to test several waste streams in more detail.”
All in-house
For this project, Baets and Van den Berg are collaborating with various academic groups that specialise in microbiology, food chemistry, bioprocess engineering and food & bio-based research. Van den Berg: “Together with other industrial partners in the BE-Basic project, we have all the expertise in-house to oversee the whole production process, from pre-treatment right through to the final purification of the lactic acid.”
All the data that are generated by the project partners will undergo a lifecycle analysis (LCA). An LCA establishes the impact of every process step on, for example, greenhouse gas emissions and other important parameters. Van den Berg: “An LCA will give us more insight into whether our production process will be sustainable and whether we’re on the right track.
” The end result will be a design on paper that describes the production process of lactic acid from non-food feedstocks. Baets: “The design will be validated on both the lab and the pilot scale, so we’ll have generated sufficient data by 2015 to target an industrial installation. But whether it really is going to happen depends on many factors.”
Started
January 2010